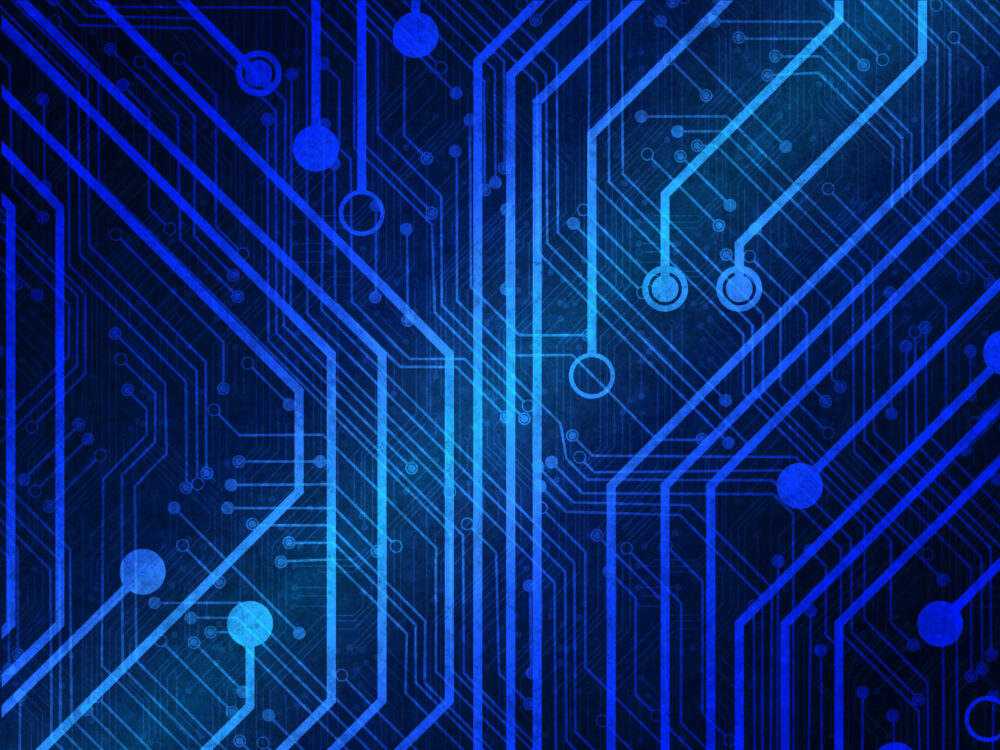
半導体とは何?わかりやすく解説します。
現在半導体不足による車の受注停止や受注できても
1年から2年待ちと言う事になっています。
今後の半導体の供給状況や国内生産の行方・製造工程・
半導体装置メーカーについて
記事をまとめてみました。
- 半導体とは
- 半導体の用途
- 半導体の大まか製造工程
- 半導体にかかわる企業
- 政府の動き
- 半導体の今後の状況
半導体とは
物質には、電気を通す導体(金、銀、銅、鉄アルミニウムなど)と
電気を通さない絶縁体(プラスチック、木、ゴム、ガラスなど)があります。
半導体(シリコン、ゲルマニウム、カーボンなど)は条件によって
電気を通したり、通さなかったりする半分導体の物質です。
マイナスの性質を組み込んだ半導体とプラスの性質を組み込んだ
半導体を作り、それを組み合わせる事でダイオード
トランジスタが出来ます。
トランジスタは一方向には、電気を通しますが
反対方向では電気を通さない性質があり
一方向で電気を通した時に光を発生します。
その性質を利用しているのが発光ダイオード(LED)です。
その反対の光を電気に変換できる性質を利用した物は
太陽光発電に使用されています。
トランジスタは、電気信号を増幅させたり電気を止めたり
流たりと、スイッチの様な役割が出来ます。
このトランジスタやダイオードを小さな基板にたくさん組み込んだ物を
集積回路(IC)と言い、ICの事を半導体と呼ぶことが多いです。
電化製品や車、パソコンの基板を見たことがあるかたもいると思います。
その中の黒い四角いムカデの様な足の沢山ある物が集積回路ICと言います。
半導体の用途
半導体の使われている用途は、パソコン、スマートフォン、
洗濯機、冷蔵庫、太陽光発電、自動車、家と
ありとあらゆる製品に使われており、半導体は生活に
欠かせない物になって来ています。
今後は自動運転やスマートシティー、AI、IOT、5G、
EV、にも続々と用途を広げています。
半導体の大まかな製造工程
- 設計工程
- ウェハー工程
- 酸化被膜生成工程
- 洗浄工程
- 感光材塗布工程
- 露光と現像工程
- エッジング工程
- イオン注入工程
- 感光材剥離工程
- 保護膜形成工程
- 検査工程
- ダイジング工程
- ダイボンディング工程
- ワイヤーボンディング工程
- モールディング工程
設計
半導体を作るうえで、どの様なことをしたいかを
電気回路により設計し、半導体の原板を作ります。
その設計の事をマスクと呼んでいます。
マスクを元に露光装置を通してウェハに回路を映していきます。
ウェハー工程
ウェハー洗浄
購入したウェハを洗浄します。
チリやほこり、油、汚れ等がない様に綺麗に洗浄を行います。
酸化被膜生成
ウェハーの表面に酸化被膜を生成します。
酸化被膜を生成するには、高温(約1000℃)の酸素の空気中にウェハーを入れて数時間かけてゆっくり酸化被膜を育てます。
シリコン結晶のウェハーに水蒸気と酸素を加え二酸化ケイ素を形成します。
二酸化ケイ素は半導体の電気を通さない部分(絶縁体)に使用します。
洗浄
シリコンウェハー上に酸化被膜を形成した後
異物が表面に付着していると、半導体としての機能が
失われてしまう可能性があるので
洗浄により塵や金属、有機物、細菌、油脂を徹底的に洗浄により除去していきます。
各工程の前や後に洗浄工程が設けられています。
感光材塗布
集積回路を形成する時にウェハーを高速で回転させ
均一に薄膜を作ります。
その薄膜にフォトマスクやレチクルを利用し、回路が描かれたガラス版に光を照射して回路を刻み込み感光材に回路を焼き付けます。この原理はフイルム写真の現像の原理と同じです。
露光と現像
微細な電子回路のパターンをガラス板に描いたフォトマスクを超高性能なレンズを重ね合わせて通し、縮小してシリコンウェハーの板に微細な回路パターンを焼き付ける工程です。
現像はウェハー上のレジストの露光された部分を薬液でとかし、溶けずに残ったレジストをレジストマスクと言い、
レジストマスクの下の層はエッジングにより腐食せずに残った部分が最終的に回路となります。
エッジング工程
エッジングとは露光現像により回路が転写された部分の酸化被膜層の部分を薬品やイオンの腐食作用を利用してシリコンウェハー部分を露出させ回路を作る工程です。
イオン注入
シリコンウェハーは電気性がないためイオンを注入することで、電気性を施す工程です。不純物(リンやホウ素など)をイオン化して高圧電で加速することで、ウェハーにイオンを打ち込みます。イオンが打ち込まれて初めて電気性の性質を持ち半導体の役割を果たす事が出来ます。
感光材剥離
ウェハーに微細なパターンを転写し、エッジング後に感光材(レジスト)を薬液により剥離除去します。
半導体には光を反射するレジストは不要なので剥離除去を行います。
レジスト剥離には、2種類の方法が在ります。
ドライタイプとウエットタイプが」があります。
ドライタイプはプラズマやオゾンを使用し剥離するタイプとアルカリ水溶液や有機アミノ酸、系ケトン系の様な有機溶剤の薬液を使用する物の2種類があります。
保護膜形成
半導体ウェハーに保護膜を形成する。
保護膜の材料として一般的にポリイミドを使用し
保護膜を形成し、このままでは電気が流れないので
電極を取り付けます。
検査
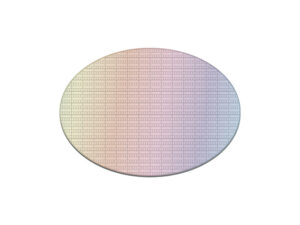
半導体の回路はとても細く人が目視検査する事が出来ないので装置により検査を行います。
ダイジング工程
1枚のウェハーには複数の回路が描かれています。
その回路を1個ずつ切り出していく工程です。
ダイボンディング
分割された半導体素子をリードフレームや基盤のチップ搭載部に接合材(はんだ、金、銀ペースト、樹脂など)で接合する工程です
リードフレームや基盤に素子を固定することが目的です。
ワイヤーボンディング
ワイヤーボンディングは集積回路(IC)の電極と基盤の電極を接続する工程です。
ワイヤーボンディングは超高速で完全自動かされており
1秒間に20箇所以上も全自動で接続出来ます。
モールディング
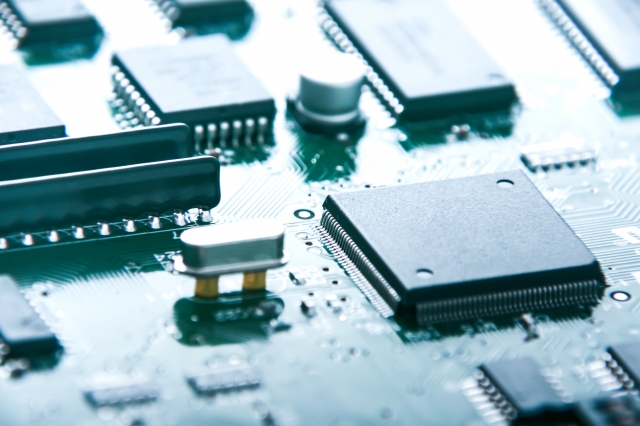
ワイヤーボンディングにより、配線が完了後した後、半導体チップを酸化やゴミから守るために
樹脂でコーティングする工程になります。
そのあと最終検査を経て半導体が完成します。
半導体装置メーカー
・酸化被膜生成装置
東京エレクトロン
・感光材塗布装置
東京エレクトロン
・洗浄装置
スクリーン
・露光装置
Canon
Nikon
・フォトマスク製造装置
ニューフレアテクノロジー
レーザーテック
・エッチング装置
東京エレクトロン
・イオン注入装置
日新イオン機器
住友重機機械イオンテクノロジー
・感光材剥離
東京エレクトロン
スクリーン
・保護膜形成
アルバック
サムコ
・検査
日立ハイテク
・ダイジング装置
ディスコ
東京精密
・ダイボンディング
BESI
ASM
・ワイヤーボンディング
ASM
キューリック&ソファ
・モールディング
TOWA
ASM
・最終検査
アドバンテスト
半導体の政府の動き
次世代半導体の新たな拠点を発表、政府が700億円の支援を行い日米で開発体制を管理して行くとしています。
700億円は半導体の開発には少ない金額ですがこれから
徐々に拡大していくようです。
微細な最先端の半導体をアメリカ始めとして、各国と有志国と連携をしながら取り組んでいく、その大きな一歩がLSTCの設立であり、ラピダスへの支援である。
新会社ラピダスとは、トヨタ自動車、NTT、ソニーグループ、
ソフトバンク、デンソー、キオクシア、NEC、三菱UFJ銀行大手8社が出資しています。
経産省は東京エレクトロン前社長が理事長を務めるLSTCの年内立ち上げ日米で合意した共同研究開発の中核を担うとしている。(2022年11月11日)
ソニーが熊本に半導体新工場を検討している。
投資額は数千億円規模とニュースで報道されています。
ソニーグループが熊本県に半導体の新工場の建設を検討している。
スマートフォンのカメラに伴う半導体の生産能力の拡大をすると言う事です。
スマートフォンのカメラに伴う半導体部品で世界シェア4割をしめています。需要の拡大を見込んで、さらに生産能力の拡大を狙っています。
2025年ごろを目処に稼働を開始する予定だと言う事です。
これとは別に同じ熊本に台湾の半導体大手TMSCやデンソーと共同で新たに半導体製造工場の建設を進めています。
(2022年12月16日)
半導体今後の半導体の状況
2022年11月15日
トヨタ自働車は半導体不足により、2023年1月に
一部工場2工場のラインを最大9日稼働の停止すると
発表しました。
半導体の長引く供給不足により、今年度1年間の世界全体の」
生産台数を、970万台から950万台に下方修正しました。
こうしたことから来年も、まだ半導体不足は解消しないと
考えられます。日本やアメリカが半導体の製造工場を建設しているので、稼働が始まれば解消していくと考えられます。
後は日本自体がどこから良質な価格の安い半導体を安定的に購入するかを考えて行かなくてはいかないと思っています。
上文でも触れていますが、熊本にTSMCの半導体工場の建設が決定し22/28ナノプロセスの半導体が生産される予定です。25年に稼働開始する計画との事です。
22/28ナノプロセスの半導体は、20ナノのカメラに搭載される先端半導体の
比べると数世代前の技術ですが、自動車や産業分野で需要が見込まれるため
ソニー、デンソー、トヨタ自動車(デンソーはトヨタのグループ会社)
を踏まえると、主にトヨタ自動車向け半導体の製造が考えられます。
稼働開始が2025年との事なので後2、3年は半導体不足が続くのではないかと
推測されます。